WASHINGTON — A little-known technology that essentially makes something out of nothing could mean cheaper, faster weapons and equipment for the Defense Department, according to some top military researchers. And the Pentagon already is embracing it.
Direct Digital Manufacturing, or additive manufacturing, uses a computer image to fabricate an item by feeding metal wires into an electron beam which melts the wires and fuses them layer-by-layer, piece-by-piece, into a finished product. At a quick pace of 15 pounds per hour, DDM can build anything from a small nozzle to an airplane wing.
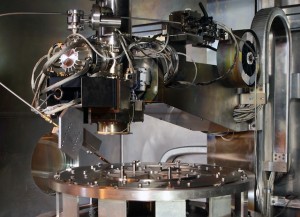
Photo Courtesy of Scaiky Inc. This additive manufacturing machine feeds wire metal into an electron beam which acts as a power source to metal and fuses the wire together to form a product. This ground-breaking technology can manufacture anything from an air seal to a plane wing.
Kenn Lachenberg, engineering manager at Scaiky Inc., a Chicago company that uses DDM in manufacturing said the quality of the DDM product is very close to that of the original product itself.
Traditionally, new parts are “machined-out” or forged into a shape out of much bigger piece of material, he said. “There’s a lot of waste with that. Plus it takes forever and the cost is phenomenal.”
The new technology minimizes waste by making the material out of as little as possible with hardly any human involvement.
“This is the industrial revolution continued,” said Larry Schuette, director of innovation the Office of Naval Research, who recently wrote an article on DDM for the Armed Forces Journal. He thinks this novel technology could have a significant future in the Department of Defense.
In fact, DOD already is pursuing it.
“Much work has been done to bring these capabilities to a point where they can practically serve the war-fighter,” the DOD stated in an e-mail. “With concerted effort, DDM has a bright future in DOD.”
The department’s efforts concentrate on rapid manufacturing of noncritical weapon’s components. “Mobile Parts Hospitals” contain DDM technology for Army systems deployed in Southwest Asia.
“In 20 years, it will be how we do business if we’re ready for it,” Schuette said. “And I think we will be.”
The sweet spot for the Department of Defense, he said, is that DDM can create a part for a machine that might otherwise be obsolete—for less money.
It would be ok to spend large amounts of money to invest in forging machines and production lines, if you’re building a lot of something, Schuette said. But because military technology is specialized and often doesn’t require one item’s mass production, DDM can save on both materials and costs.
“We have an opportunity to use DDM because of the flexibility it provides and because the quantities that we need are potentially lower.”
The new technology can also be used to build up an area that has been worn or needs repair, he said. Engine air seals, for example, can wear over time, and cost a lot to replace. DDM can build the area that is worn and avoid extra costs, Lachenberg said.
Defense contractors such as Lockheed Martin Corp. and Boeing Inc., both of which ranked within the top three U.S. defense companies in 2011, have embraced DDM.
Lockheed Martin, which has experimented with DDM for about 10 years, has been using the technology to manufacture non-mission critical components and to make models and prototypes.
“A key benefit from DDM technology is more efficient production of complex geometries,” Jeffery Adams, Lockheed Martin spokesman said. “It also allows us to minimize our material waste, saving our industry raw material costs and energy costs, and supporting our corporation’s sustainability goals.”
Sciaky was awarded two Phase II Small Business Innovative Research projects through the Air Force for refining the DDM process—the first for$4.5 million and the second for $750,000. The second specifically addressed the development of the EBDM Closed Loop Control process through the Air Force.
Boeing is a subcontractor to both Sciaky—on a SBIR program—and Lockheed Martin—on a Department of Defense program—to implement DDM technology.
It has been developing work in additive manufacturing since 1997, but does not use the technology on current aircraft programs.
“We do use them widely in the production of prototype parts to perform form, fit and function tests,” Daryl Stephenson, Boeing spokesperson said. “In the future, we expect to be using additive manufacturing for components on both military aircraft and commercial airplanes.”
The speed of the process, reproducibility and quality of the finished product all need to be perfected before DDM can be a reliable system. There are no norms or standards for additive manufacturing, Stephenson said, which prevents more widespread use of the technology—for now.
It’s a learning process still, Schuette agreed, but testing is showing progress.
“It really is the future of the commercial world and it will be the future of the defense manufacturing as well,” he said.